
Part C Project
"New Sub Assembly Line Design & Integration in an Automotive Environment​.
In partnership with Bentley Motor Limited".
Problem:
-
Launch of the new Bentley Bentayga SUV into production, requiring all production areas to be optimally designed & set up before this happens.
-
The rational of this project has been to determine the most suitable location, method of delivery & system to provide the assembly of the Bentayga’s fenders & integrate them back into the main already established production line, in a restricted build hall.

Research:
-
To gauge theoretical background theory, the current methods & thought process in the design of automotive production lines & the uses of lean considerations in manufacturing were explored.
-
Additionally, looking at the trends in the automotive market & what future considerations would need to be made, including a review of computer based simulation methods that could be used to optimise & refine the production layout.

Bentley production & demand increasing
http://www.statista.com/statistics/386352/british-luxury-car-brand-bentley-global-production-volume/
Limitations:
-
Main line runs at 17.5 minute takt time, must not impact this time.
-
Line side space limitation for fixture of 2000x1800mm footprint & selected area build constraints.
-
Decision between; all-in-one build fixture & transportation dolly or use of existing static build fixture & simpler transportation dolly.
-
All designs must adhere to company visual & transposition standards as will be moved manually & via a Tow-motor.

Design:
-
Configuration of bespoke parts stillage rack for the 12 parts require in the build.
-
Varied concept development of fixture/transportation dolly & review against the 51 point specification, with additional company feedback.
-
Generation of precise CAD model of final design with production of 1:10th scale representative model.
-
Ergonomic assessment of design with selected operator characteristics.
-
Critical examination of concern areas (FMEA) for conformation of proposal & suggested design improvements.
-
Detailed costing & material choice review of all parts in design for later comparable costing evaluation.
-
Supplier quotation to show proposals budget adherment & implementation strategy.

Area flow:
-
Review of 2 different area locations & their potential.
-
Analysis of different flow, layout patterns & operator movement.
-
Timing measurement analysis of the proposed system for optimisation.
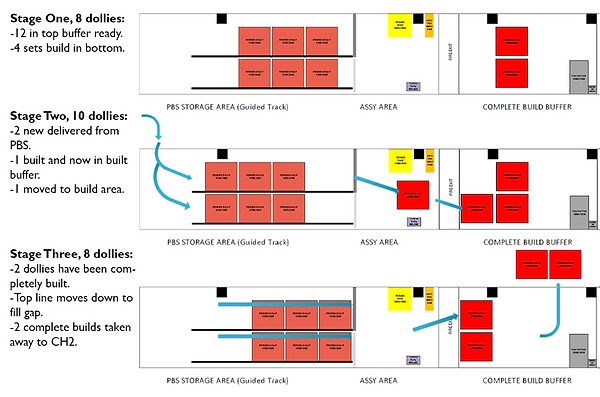
Outputs:
-
Design of a bespoke, handed, carousel, all-in-one fixture that carries four fenders through the entirety of the system.
-
A fully functioning system that has the capability to move, build & deliver the fenders 22 stations later down the line
-
Throughput time (fixture set, PBS ST1-CH2 ST13): 286.00 minutes (takt+loading+transport)
-
System time (fixture set to return to original position/ whole rotation): 347.75 minutes
-
Scope to be reduced in takt time by 28.50% & integrated safety buffers at both ends of the sub-assembly.
-
Linear sub-assembly area that can hold & flow up to 24 sets of vehicle fenders & allow easy logistical delivery of parts & interaction with fixtures.

Future:
-
Details of all the findings will be handed over to the ‘Production Planning’ team and the BY63X production line manager for review, with the scope of integration if accepted.
